Products > Gaskets > Non-Metallic Gaskets > Rubber Gaskets > EPDM Gasket
EPDM Gasket Material
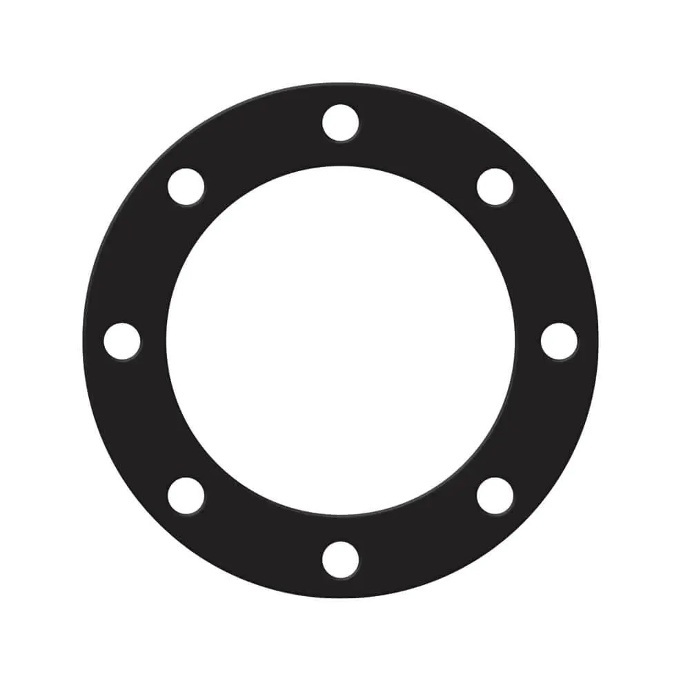
Rubber EPDM gasket material with good resistance to moderate caustics and excellent resistance to low pressure steam, hot water, ozone and UV aging. EPDM is available in two common grades; Sulfide Cured and Peroxide Cured as detailed below.
EPDM Gasket Thomson Style 563 (Sulfide)
Sulfide cured is considered a “standard grade” and has basic chemical and temperature resistance.
EPDM Gasket Thomson Style 6965 (Peroxide)
Peroxide cured EPDM gasket with superior chemical compatibility and temperature resistance to 300°F. Style 6965 also has superior resistance to compression set and will retain resilience for longer periods in service. Peroxide Cured EPDM is used extensively in the Chlorine, Caustic and Bleach industries.
- Temperature: -70°F (-56°C ) to 250°F (121°C).
- Pressure: 250 psi.
- Suggested uses: Saturated, low pressure steam, Hot Water, Brake Fluid, Dilute Alkalines.
- Not suitable for: Any petroleum-based media, Petroleum Fuels, Diester lubricants.
EPDM Gasket Material Guide
EPDM (ethylene propylene diene monomer) is a versatile synthetic rubber material widely used in various industries for sealing applications. EPDM gaskets are known for their excellent resistance to weathering, ozone, UV exposure, and aging, making them suitable for outdoor and harsh environments. Here's everything you need to know about EPDM gasket material:
1. Properties of EPDM Gasket Material:
-
Excellent Weather Resistance: EPDM gaskets can withstand extreme weather conditions, including sunlight, rain, snow, and temperature fluctuations.
-
Chemical Resistance: EPDM is resistant to a wide range of chemicals, including acids, alkalis, and polar solvents, making it suitable for diverse industrial applications.
-
Temperature Resistance: EPDM gaskets offer good performance over a wide temperature range, from -50°C to 150°C (-58°F to 302°F).
-
UV and Ozone Resistance: EPDM gaskets have excellent resistance to UV radiation and ozone exposure, ensuring long-term durability in outdoor applications.
-
Electrical Insulation: EPDM exhibits good electrical insulation properties, making it suitable for sealing electrical enclosures and components.
2. Applications of EPDM Gasket Material:
EPDM gaskets find applications across various industries, including:
-
Automotive: Commonly used in automotive applications, such as sealing doors, windows, and engine components, due to their weather resistance and durability.
-
Construction: Used in building construction for sealing windows, doors, roofing, and HVAC systems.
-
Electronics: Utilized in electronic enclosures and devices to provide environmental sealing and protection against moisture and dust.
-
Industrial Machinery: Used in industrial machinery for sealing fluid and gas systems, pumps, valves, and other components.
-
Marine: Suitable for marine applications due to their resistance to saltwater, UV radiation, and weathering.
-
Aerospace: Used in aerospace applications for sealing aircraft components and systems.
3. Manufacturing Process:
EPDM gaskets are typically manufactured using compression molding or extrusion processes. The steps involved in the manufacturing process include:
-
Formulation: EPDM rubber is compounded with additives and fillers to achieve desired properties such as hardness, elasticity, and resistance to environmental factors.
-
Molding/Extrusion: The compounded EPDM material is shaped into gaskets using compression molding or extrusion techniques.
-
Curing: The molded or extruded gaskets are subjected to heat and pressure in a curing process to cross-link the polymer chains, imparting strength and stability to the material.
-
Finishing: After curing, the gaskets may undergo additional processes such as cutting, trimming, and surface treatment to meet specific dimensional and performance requirements.
4. Selection Considerations:
When selecting EPDM gaskets for a particular application, consider the following factors:
-
Temperature Range: Ensure that the EPDM gasket material can withstand the operating temperatures of the application.
-
Chemical Compatibility: Verify that the EPDM material is compatible with the chemicals and fluids present in the application environment.
-
Compression Set Resistance: Choose EPDM gaskets with low compression set to maintain sealing integrity over time.
-
Hardness: Select the appropriate hardness (durometer) of EPDM material based on the sealing pressure and surface roughness of mating components.
-
Dimensional Stability: Ensure that the EPDM gaskets exhibit good dimensional stability to maintain sealing effectiveness under compression.
-
Environmental Exposure: Consider the exposure to UV radiation, ozone, weathering, and other environmental factors relevant to the application.
5. Installation and Maintenance:
Proper installation and maintenance practices can enhance the performance and longevity of EPDM gaskets:
-
Surface Preparation: Clean and prepare the sealing surfaces to ensure proper adhesion and sealing.
-
Compression: Apply the recommended compression force to achieve a proper seal without over-compressing the gasket.
-
Inspection: Regularly inspect EPDM gaskets for signs of wear, damage, or degradation, and replace them as needed.
-
Storage: Store EPDM gaskets in a cool, dry environment away from direct sunlight and ozone sources to prevent premature aging and deterioration.
6. Environmental Considerations:
EPDM gasket material is considered environmentally friendly due to its durability, recyclability, and low toxicity. However, proper disposal practices should be followed to minimize environmental impact.
Conclusion:
EPDM gasket material offers excellent weather resistance, chemical resistance, and temperature stability, making it suitable for a wide range of sealing applications across various industries. By understanding the properties, applications, manufacturing process, selection considerations, and installation/maintenance practices outlined in this guide, you can effectively utilize EPDM gaskets to achieve reliable and long-lasting seals in your specific applications.